If you're like many manufacturing leaders in the Midwest today, you're probably feeling the pressure to modernize while keeping costs under control. Let's face it—digital transformation isn't just a buzzword anymore, it's becoming essential for survival. In this guide, I'll break down how IoT digital twins can be game-changers for your business, whether you're running a small machine shop or managing multiple production facilities.
IoT Digital Twins: Integration Approaches for Small vs. Large Manufacturers

Jump ahead to:
- How Digital Twins Can Transform Your Manufacturing Process
- Understanding What's Available Today
- Challenges You'll Face as a Small Manufacturer
- Challenges You'll Face as a Large Manufacturer
- Strategies That Actually Work (Based on Your Company Size)
- Getting It Right: Best Practices You Can Actually Use
- What's Coming Next (And How to Prepare)
- Finding Your Path Forward with IoT Digital Twins
The Power of Virtual Replicas
Let me guess—you've heard people talking about "digital transformation" at trade shows and in industry publications, but you're wondering what that actually means for your day-to-day operations. Let's cut through the jargon and discuss two technologies that could genuinely change how you run your business: IoT (Internet of Things) and digital twin technology.
You're probably thinking, "Great, more tech buzzwords I need to decipher." I get it. Let me break it down in plain English.
IoT is basically getting your equipment to talk to you and to each other. Imagine if your CNC machine could tell you exactly how it's performing, if it's running too hot, or when it needs maintenance—without you having to check it physically. That's IoT in action: your machines, vehicles, and real-world equipment all communicating automatically and giving you updates about what's happening on your shop floor.
Digital twin technology creates a virtual copy of your physical equipment or processes. Think of it as having a digital duplicate of your production line that you can experiment with. Want to see what happens if you rearrange your workflow? Test it on the digital twin first. Worried about how a new process might affect quality? Try it with a virtual representation before implementing it in real life. It's like having a risk-free testing ground for your entire operation.
Together, these technologies give you something you've probably always wanted: clear visibility into every aspect of your business and the ability to make improvements without disrupting production. IoT gathers the data from your equipment, and digital twins help you make sense of it all, showing you exactly where you can cut costs, improve efficiency, and drive innovation.
How Digital Twins Can Transform Your Manufacturing Process
Picture this: You're walking through your facility and you can see potential problems before they happen. You know exactly which machine needs maintenance next week, not because it's on some arbitrary schedule, but because the data tells you it's starting to show signs of wear. That's what digital twins, powered by IoT sensors, can do for your operation.
With this technology working for you, you'll be able to:
Keep an eye on your equipment 24/7, even when you're not physically there
Spot problems brewing before they turn into expensive breakdowns
Make decisions based on actual data, not hunches or outdated schedules
Think about how much money you lost the last time a critical machine unexpectedly broke down. Now imagine cutting those kinds of disruptions by 30-50%. That's not a made-up number—it's what other manufacturers have achieved with this technology. Plus, you can extend the useful life of your equipment by 20-40%, getting more value from the capital investments you've already made.
Want to try a new production layout? You could shut down for a day to rearrange everything, only to find it doesn't work as well as you hoped. Or you could test it virtually first, using your digital twin. Need to figure out the most efficient way to run a particular job? Simulate different scenarios and find the sweet spot that maximizes output while minimizing energy use and equipment wear.
The bottom line? You'll run a tighter ship with fewer surprises, lower costs, better quality, and the ability to respond quickly when opportunities or challenges arise. In today's competitive market, that kind of edge can make all the difference between struggling to keep the lights on and confidently growing your business.
Understanding What's Available Today
The Tools and Technology at Your Fingertips
Remember when the only "smart" device in your shop was the coffee machine with a timer? Those days are long gone. Today, you can outfit your operation with sensors, connected machines, and monitoring systems that give you unprecedented visibility into what's happening on your floor. These tools can track almost anything in the physical world—machine performance, product quality, maintenance needs, worker safety, inventory levels, and even energy usage.
You don't need to build these systems from scratch, either. Major tech companies have developed platforms specifically for manufacturers like you. Microsoft Azure IoT Operations, for instance, offers industrial-grade capabilities that help bridge the gap between your operational technology (the machines and equipment) and information technology (your computer systems). It's designed to make the transition manageable, even if you're not an IT expert.
Oracle offers similar solutions with their IoT Production Monitoring Cloud Service, which helps you manage work orders or production processes in real-time to keep track of everything happening in your facility. These platforms are becoming more user-friendly, so you don't need a computer science degree to start using them.
What Other Industries Can Teach Us
You might be surprised to learn that some of the most innovative uses of digital twins aren't happening in manufacturing at all. Healthcare providers are creating virtual replicas of patients—combining health records, genetic information, and sensor data—to test treatments before trying them on real people.
Automotive companies are using digital twins to test product designs virtually before building physical prototypes. This saves them time and money while also improving safety. They're also using digital twins to predict when vehicles will need maintenance, just like you might want to do with your manufacturing equipment.
What does this mean for you? These examples show that digital twin technology is mature enough to deliver real results across different industries. The same benefits these other sectors are seeing—better planning, reduced downtime, improved efficiency—are available to your manufacturing operation as well.
Challenges You'll Face as a Small Manufacturer
The Budget Reality Check
Let's be honest—when you're running a smaller operation, every dollar counts. You're probably wondering if you can actually afford to implement IoT and digital twin technologies. Here's what you need to consider:
Hardware costs: You'll need to invest in sensors, devices, and possibly infrastructure upgrades
Software expenses: Custom applications, dashboards, and interfaces are an investment
Analytics tools: The real power comes from making sense of the data, which requires specialized software
Monthly connectivity bills: Your devices need to talk to each other, and those data plans add up
Ongoing maintenance: Expect to spend 15-25% of your initial investment each year on updates and support
I won't sugarcoat it—even a basic IoT implementation (what techies call a "minimum viable product") typically runs $30,000-$50,000. If you want all the bells and whistles with advanced analytics and machine learning, you could be looking at $100,000 or more.
For you, the challenge isn't just finding the money—it's figuring out how to allocate your limited resources across hardware, software, and analytics while still keeping your day-to-day operations running smoothly.
Why Predictive Maintenance Should Be Your First Priority
Despite these costs, there's one application that's worth every penny for smaller shops: predictive maintenance. Think about this sobering number: unplanned downtime can cost up to $260,000 per hour. For a business your size, a single major equipment failure could be devastating.
By implementing even a basic IoT solution system focused on predictive maintenance, you could:
Cut unexpected downtime by 30-50% (imagine what that would do for your delivery schedules)
Get 20-40% more life out of your expensive equipment
Know exactly what's happening with your machines, even when you're not on the floor
Address problems before they turn into crises
Schedule maintenance when it's convenient for you, not when something breaks
Make your equipment investments last longer
You don't need to wire up your entire facility at once. Start with wireless sensors on your most critical equipment—the machines that would cause the biggest problems if they failed. These sensors can track vibration, temperature, moisture, and other indicators that something's going wrong, even in parts of your equipment that are hard to check manually.
To measure your success, keep an eye on metrics like Mean Time to Repair (MTTR) and Mean Time Between Failures (MTBF). In plain English, these tell you how quickly you're fixing problems and how often your equipment is breaking down—both numbers you want to improve.
Challenges You'll Face as a Large Manufacturer
Wrangling Data From Multiple Systems and Locations
If you're managing a larger operation with multiple production lines or facilities, you've got a different set of headaches. Your challenge isn't just paying for the technology—it's getting all your systems to play nicely together. Here's what you're up against:
Too many data sources: Your Manufacturing Execution Systems (MES), SCADA systems, and Human-Machine Interfaces are all speaking different languages
Format frustrations: Some systems use JSON, others use XML or CSV, making it hard to get a unified view
Protocol problems: Each system might use different communication protocols, creating connection nightmares
Vendor variety: When you've bought equipment from different vendors over the years, getting them to communicate can be like hosting a meeting where everyone speaks a different language
Old meets new: That equipment you bought in the '90s wasn't designed for IoT connectivity
Data overload: The sheer volume of information coming in can overwhelm your existing systems
Solving these issues isn't simple. You might need middleware to bridge the gap between older and newer systems, open standards like MQTT and OPC UA to improve compatibility, cloud services to handle all that data, and edge computing to translate between incompatible formats.
You might also want to get involved with industry groups like the Industrial Internet Consortium (IIC) or the Open Manufacturing Platform (OMP) that are working on standardization. Your voice at the table could help shape solutions that work for businesses like yours.
Turning Real-Time Data Into Your Competitive Edge
The flip side of managing all this complexity is the tremendous advantage you'll gain from having real-time data at your fingertips. Imagine seeing production issues the moment they occur, spotting market trends as they emerge, and identifying operational bottlenecks instantly rather than discovering them weeks later in a report.
With predictive analytics, you can take things even further. Instead of just reacting to what's happening now, you can anticipate what's coming next—forecasting maintenance needs, predicting customer orders, and optimizing your marketing efforts based on actual data rather than guesswork.
The practical benefits are substantial: you'll be able to monitor your key performance indicators continuously, quickly identify where you're wasting resources, and optimize how you allocate people and equipment. You can even personalize your customer interactions based on real-time analysis of their behavior and preferences.
Yes, implementing these systems requires significant investment in technology and skilled personnel. But when you consider the long-term benefits—reduced downtime, better decision-making, and improved performance of the physical systems across your entire operation—it's an investment that can pay dividends for years to come.
Strategies That Actually Work (Based on Your Company Size)
For Small Manufacturers: Start Small, Think Big
If you're running a smaller operation, I have good news: you don't need to transform your entire facility overnight. Instead, think of IoT implementation as a journey that starts with a single step. A modular approach lets you begin with what matters most and grow as your business evolves.
Here's what that might look like for you:
Start with programmable sensors on your most critical equipment
Add data collection tools that give you real-time information about what's happening
Implement local processing devices so you don't need to send everything to the cloud
Eventually add cloud connectivity for more comprehensive analysis and remote access
The key is to begin with a focused approach that addresses your biggest pain points, then build from there as you see results and your comfort level grows.
Let me share some real use cases from businesses probably a lot like yours:
- A machine shop in Ohio installed IoT sensors on their CNC machines to monitor vibration and temperature. They started with just their three most critical machines. When those sensors helped them detect early signs of wear and schedule maintenance proactively, they reduced unexpected downtime by 30%. Encouraged by this success, they gradually expanded the system to include their entire shop floor
- An electronics manufacturer in Michigan added IoT-enabled cameras and sensors for quality control on a single production line. When automated visual inspections detected defects in real-time, product quality improved by 25%, dramatically reducing waste and rework. Seeing these results, they gradually expanded to other production lines.
- A furniture maker in Indiana put RFID tags on their high-value inventory items, enabling real-time tracking that reduced both stockouts and overstock situations. Their order fulfillment efficiency increased by 20%, so they expanded the system to track all inventory.
The beauty of this approach is that you can implement it cost-effectively, improve your efficiency step by step, enhance your quality control, manage your resources better, and gain competitive advantages through data-driven insights—all without breaking the bank on large upfront investments.
For Large Manufacturers: Building Your Ecosystem
If you're managing a larger operation, your approach will naturally be more comprehensive. You need enterprise-level IoT strategies that not only improve your internal operations but also enhance your customer experiences and potentially contribute to broader initiatives in your community.
Your IoT implementation will likely span multiple facilities and integrate with your supply chain, focusing on improving product quality and customer satisfaction through real-time quality control, predictive maintenance, and supply chain optimization.
You'll need sophisticated visualization tools to make sense of all this complexity:
Digital twin technology creates virtual replicas of your physical assets and processes, giving you real-time monitoring, predictive data analytics, and scenario planning capabilities without disrupting actual operations.
Enterprise-level IoT platforms like Hitachi's Lumada that offer centralized control, real-time analytics, and customizable visualizations of your diverse IoT devices and data streams.
With approaches like these, you're not just enhancing your internal operations—you're creating new ways to engage with customers and potentially contributing to the development of smarter, more efficient communities in the regions where you operate.
Getting It Right: Best Practices You Can Actually Use
Managing Your Data and Devices for the Long Haul
No matter the size of your operation, there are some fundamental practices that will help you succeed with IoT implementation:
Making Your Data Work For You:
Start with clear goals that connect directly to your business needs (like reducing downtime or improving quality)
Check your data quality early—garbage in means garbage out
Pick the right approach for moving data between systems (whether that's batch processing, APIs, or event-triggered updates)
Make sure your solution can grow with you by using cloud platforms that can scale up when needed
Don't set it and forget it—regularly check that your systems are still working as intended
Taking Care of Your IoT Devices Through Their Lifecycle:
When You're Getting Started: Carefully assess what you need and how to set it up securely
During Daily Operations: Keep an eye on performance, update your devices regularly, and use edge computing when it makes sense
When It's Time to Replace: Make sure you decommission old devices securely and dispose of them properly
Finding Hidden Gold in Your Data
Once you have IoT systems up and running, you'll start discovering opportunities you might not have even considered:
Smarter Decisions: Use actual data, not gut feelings, to guide your sustainability efforts and optimize how you use resources
Better Supply Chains: Find more sustainable sources for your materials and improve your transportation efficiency to reduce your carbon footprint
Environmental Awareness: Monitor your impact on air and water quality so you can make improvements where needed
Energy Savings: Use sensors to adjust equipment settings in real-time, optimizing your energy use without sacrificing performance
Waste Reduction: Catch resource waste as it happens—like identifying water leaks immediately instead of discovering them on your utility bill
By following these practices, you'll not only improve your current operations but also uncover new opportunities to make your business more efficient and sustainable. The data you collect today could reveal the innovations that will keep you competitive tomorrow.
What's Coming Next (And How to Prepare)
Tomorrow's IIoT Trends That Will Impact Your Bottom Line
Looking ahead to 2025, several developments in Industrial Internet of Things (IIoT) are going to change how you run your operation:
AI That Actually Works: By 2025, artificial intelligence won't just be a buzzword—it'll be essential. In fact, 93% of manufacturers already recognize AI's role in driving growth. For you, this means smarter systems that can predict maintenance needs, optimize your production schedules without human intervention, and give you visibility into your supply chain like never before.
Energy Management That Pays For Itself: IIoT is already transforming how manufacturers handle energy costs through real-time monitoring, automatic identification of waste, and smart adjustments to improve efficiency. Think about lighting systems that adjust base
Finding Your Path Forward with IoT Digital Twins
Whether you're a small machine shop in Indiana or a large automotive supplier in Michigan, IoT digital twins offer transformative potential for your manufacturing operations. The key is finding the right approach for your specific needs and resources.
For small manufacturers, start small with modular solutions that target your most critical pain points, whether that's unexpected downtime, quality control issues, or inventory management. As you see results and build confidence, expand your implementation incrementally.
For large manufacturers, focus on developing comprehensive strategies that integrate across your organization and leverage advanced visualization tools to manage complex systems effectively. Consider how your IoT ecosystem can enhance customer experiences and potentially contribute to broader initiatives beyond your factory walls.
Regardless of size, follow best practices for data integration and device management, and stay alert to the opportunities that IoT data reveals for improving efficiency and sustainability. The manufacturers who successfully navigate these digital transformations won't just keep the lights on—they'll illuminate new paths to growth, innovation, and competitive advantage in an increasingly connected world.
The future of manufacturing belongs to those who can bridge the physical and digital realms effectively. With IoT digital twins, that future is within reach for manufacturers of all sizes.
Published by Jason Hehman in Digital Twins
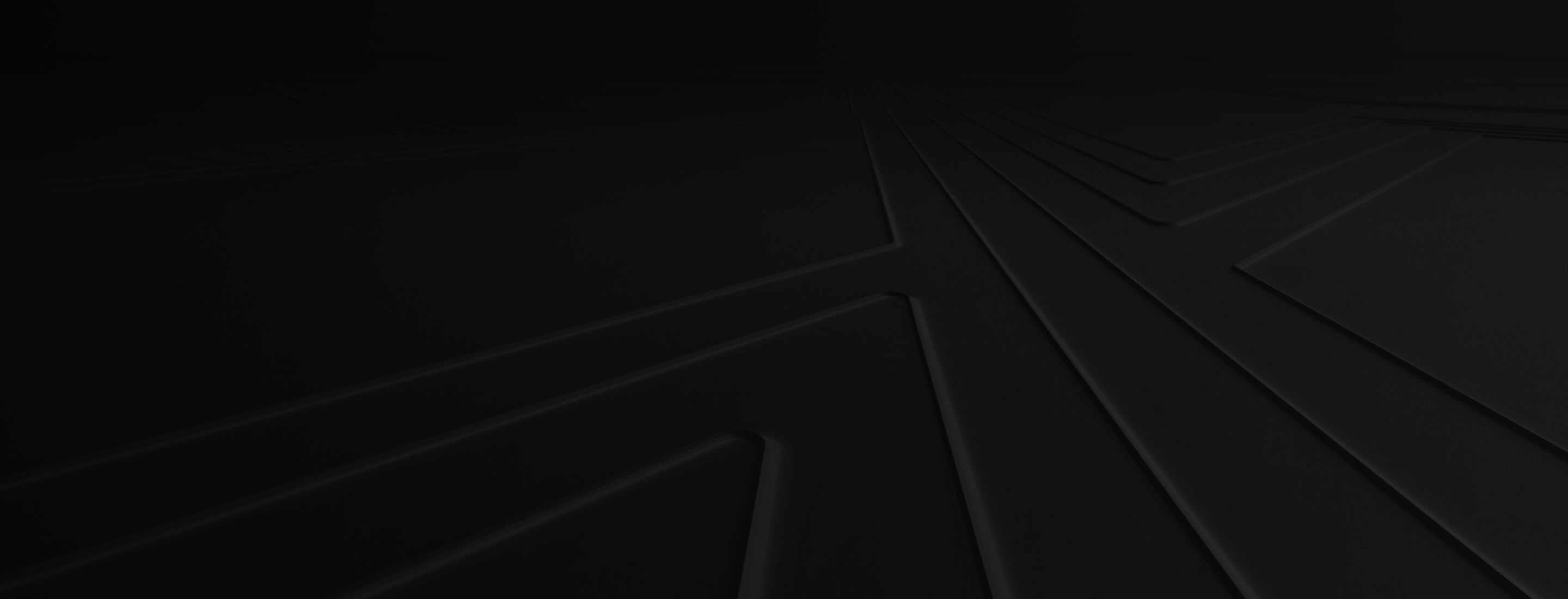
Let's shape your insights into experience-led data products together.