HS Inc. is a success story. Founded in 1969, close to Detroit, Michigan, HS Inc. started as a mold maker for the automotive industry. As the industry changed, HS Inc. changed too. They used their know-how to pivot towards making modular systems that could be easily adapted by various industries– yes, even machines that make sheet cake. Here's how they did it:
Future-proofing automation: HS Inc.’s journey

Hear HS Inc.'s journey
Modular Mainframe System
HS, Inc.'s modular mainframe system is a big part of its successful evolution. They make automation systems that are about 50% “off the shelf” and 50% based on clients’ exact needs.
This modular system benefits HS because they can easily reproduce the “off the shelf” part of the system, speeding up their own design and production process.
The modular system brings value to HS’s clients because they can switch out the customized parts based on their needs. For example, a door manufacturer might make 50 different door panels. They can exchange certain parts rather than needing separate machines for each type. This saves on floor space, improves efficiencies, etc.
Data Readiness
HS is now in the process of creating a next-generation modular mainframe system, one that has Industry 4.0 readiness baked in. It will come with data output so manufacturers can easily collect the data they need, using it to power insights and maybe even AI integrations in the future.
According to HS’s Director of Business Development, Paul St. Louis, this is how HS plans to help other companies future-proof themselves. In order to implement any technological advancements in manufacturing, companies need data. They need high-quality data and a baseline on which to make business decisions. Too often, companies try first to buy new technology, then establish data gathering and analysis, and then hope it all solves a business problem.
HS’s next-generation modular mainframe systems will have data readiness baked in so companies are future-proofed from the beginning.
Digital Twins
HS uses digital twins in its design processes. They do robot simulations at the beginning of their projects, creating a digital twin and simulating an entire manufacturing line. Then, they plug the sim data into the robot, eliminating the need for programming.
What is a digital twin?
As automation integrators, this is typically where HS’s use of digital twins stops. Still, they work with companies that use digital twin technologies to do remote troubleshooting, preventative maintenance, and maybe even workforce training one day.
HS Inc. is a great example of how businesses can adjust to factors beyond their control, using data and technology to pivot toward new success.
Published by TXI in Digital Twins
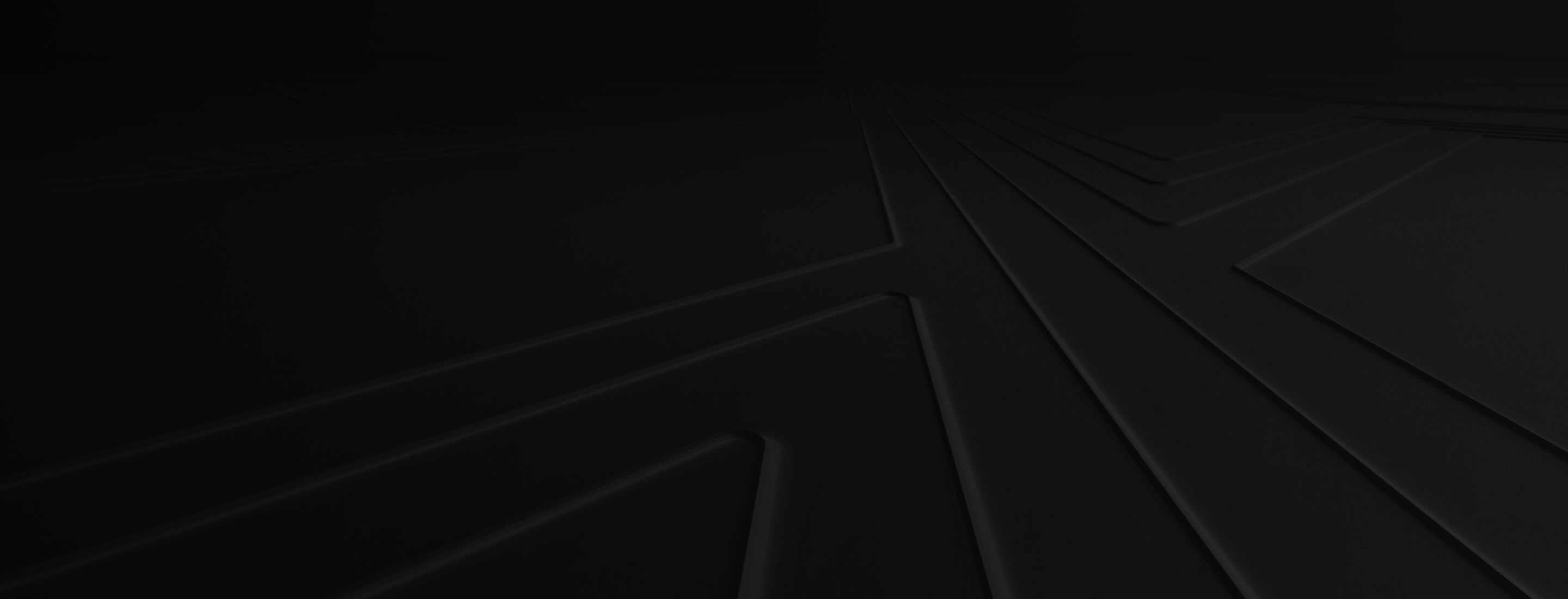
Let's shape your insights into experience-led data products together.