Today's factories and production floors have no shortage of data. Sensors hum across every line, IoT devices stream continuous signals, and enterprise systems like MES (Manufacturing Execution Systems) and ERP (Enterprise Resource Management) collect more metrics than ever before. Yet, despite this abundance, many manufacturers still aren't seeing the breakthroughs they expect. There's a common misconception here: that collecting data automatically translates into intelligence. It doesn't.
Manufacturing Intelligence Isn't Data—It's What You Do With It

Manufacturing intelligence isn't about how much data you have — it's about how you use the data analysis to make faster, more informed decisions. In fact, IoT applications in manufacturing could generate an economic impact of up to $3.7 trillion per year by 2025. In today's competitive landscape, effectively harnessing this data is what sets leaders apart.
The operations manager stared at the dashboard on her screen, awash in colorful charts and real-time metrics from the factory floor. Despite the sophisticated sensor network and data collection systems her company had invested in, she still couldn't answer the production director's most pressing question: "Why did efficiency drop 15% on Line 3 last week when all the other lines maintained their targets?"
This scenario plays out daily across manufacturing operations worldwide. Companies have enthusiastically embraced data collection—installing sensors, implementing MES systems, and building data lakes—only to find themselves drowning in numbers without the insights needed to drive meaningful improvement.
The Data Abundance Paradox
Manufacturers today are "data rich, insight poor."
With IoT sensors, connected machines, ERP platforms, and MES systems, data is everywhere. Machine uptime, energy usage, supplier performance, cycle times — every detail is captured. But too often, this data sits in silos or floods dashboards without offering clarity.
According to a 2024 Deloitte report, while 81% of manufacturers have increased investments in data collection capabilities, only 38% report having mature strategies for using this data to improve decision-making processes. The result? Missed opportunities, delayed reactions, and avoidable downtime. The challenge isn't collecting data — it's making that data work harder.
"We have sensors on virtually everything, but we're data rich and insight poor," explained a manufacturing director at a Midwest automotive supplier. "When executives ask why a particular metric is trending in the wrong direction, we spend days piecing together information from different systems before we can provide an answer—and by then, the problem has either resolved itself or gotten worse."
With U.S. manufacturing capacity utilization climbing to 77.0% in mid-2024—still below its long-term average—there's clear pressure on manufacturers to optimize operations and reclaim performance gaps.
What Defines True Manufacturing Intelligence
At TXI, we often describe manufacturing intelligence through the DIKW model: data, information, knowledge, wisdom.
Raw data, like machine readings and sensor logs, forms the foundation. Information organizes this data into dashboards or summaries. Knowledge goes a step further, identifying patterns and trends. And wisdom provides the best course of action, helping teams respond in real time.
True manufacturing intelligence does more than report what's happening. It delivers data-driven insights that are relevant, timely, aligned to your goals, and — most importantly — actionable. When these qualities come together, data stops being a burden and becomes a competitive advantage.
Data is simply raw facts and figures without context—sensor readings, production counts, cycle times, or temperature measurements.
Information is data that has been processed to provide context and meaning—such as trend lines showing how cycle times compare to targets, or dashboards visualizing production process efficiency across different lines.
Knowledge goes further by identifying patterns and relationships between different information sets—understanding why certain conditions lead to specific outcomes.
Wisdom represents the highest level where the system can recommend or even automate optimal actions based on deep understanding—this is where predictive maintenance and prescriptive analytics tools create their greatest value.
When a shift supervisor receives an alert that a particular machine is showing early signs of bearing wear similar to patterns that preceded three previous failures—along with a recommendation to schedule maintenance within the next 48 hours—that's manufacturing intelligence in action.
From Manufacturing Data to Intelligence: The Transformation Process
Turning raw data into manufacturing intelligence isn't a one-step move — it's a progression.
First, manufacturers need to ensure ecosystems are connected, integrating machines, sensors, and platforms so data flows seamlessly. This often requires robust data integration solutions to connect disparate systems and overcome data silos. Once the foundation is in place, the focus shifts to contextual analysis. It's not enough to process data — it needs to be meaningful within the context of your manufacturing operations.
This is where algorithms play a crucial role, helping structure and analyze data to enhance functionality across systems. Visualization tools bring these insights to life. Whether you're on the plant floor or in the executive suite, seeing the right data at the right time empowers better decisions.
Decision support systems, powered by data analytics and machine learning, take it further by recommending or automating responses. And with continuous learning loops in place, operations refine over time, turning initial gains into lasting improvements.
For many organizations, building a data warehouse becomes a critical step in this journey—creating a unified, trusted source for analytics that combines information from multiple operational systems.
The transformation follows these key stages:
1. Data Collection and Integration
The foundation begins with gathering manufacturing data from diverse sources and integrating them into a unified data environment.
2. Contextual Processing and Analysis
Raw data becomes valuable only when processed within the right context. A Midwest industrial equipment manufacturer discovered that minor temperature variations in their paint booth—well within acceptable ranges—strongly correlated with warranty claims six months later.
3. Visualization Through Effective Interfaces
Even the most profound insights deliver no value if they're not communicated effectively. Advanced visualization technologies including spatial computing are transforming how operators interact with manufacturing intelligence.
4. Decision Support and Workflow Integration
True intelligence doesn't just inform—it enables and improves decisions. This stage connects insights directly to actions through business process automation.
5. Continuous Learning and Refinement
Manufacturing intelligence isn't static—it evolves as processes change, new data becomes available, and the organization learns.
Beyond Tools: Balancing Technology and Manufacturing Process
It's tempting to see technology as the full solution. But even the best systems fall short without the right processes and people behind them.
"We spent millions on an advanced analytics platform before realizing we hadn't defined the decisions we needed to improve," admitted a manufacturing VP. "It was like buying an expensive telescope before deciding what we wanted to observe in the sky."
Manufacturing intelligence thrives when automation and human judgment work together. Automation handles routine data-heavy tasks, while humans bring strategic oversight and adaptability.
At TXI, we emphasize this balance to ensure that technology serves people — not the other way around. This human-centered approach to smart manufacturing ensures that technological capabilities enhance rather than replace human expertise.
This balance is especially critical in smart factory environments. According to a 2024 Deloitte study on Industry 4.0 adoption, 67% of manufacturing leaders cited "people and process challenges" as bigger barriers than technology limitations.
The human element cannot be overlooked—effective employee retention strategies are essential when implementing advanced analytics. The same Deloitte study found that manufacturers with formalized upskilling programs for existing employees achieved 41% higher ROI on their smart factory investments compared to those who primarily hired new talent with technical skills.
Case Studies in Action
Real-world examples show how manufacturing intelligence delivers real outcomes.
Dickson: Proactive Environmental Monitoring
Dickson worked with TXI to transform its environmental monitoring from analog systems to a connected, intelligent platform. The result? 24/7 oversight, real-time visibility, and full compliance with FDA standards for data integrity.
"TXI created the technology behind our flagship product. It's the backbone of what we'll move forward with," said Matt McNamara, VP of Products at Dickson.
By connecting data sources and enabling proactive monitoring, Dickson turned environmental data into an operational advantage. The platform integrates data from multiple sensor types, with seamless connectivity across systems that make it accessible through both web and mobile interfaces. This comprehensive approach to data integration transformed how Dickson's customers monitor critical environments, particularly in regulated industries where compliance documentation is essential.
Motorcity Systems: Connecting Drivers and Data
Motorcity Systems partnered with TXI to develop a mobile app that connects over 3.5 million truck drivers. This innovation didn't just enhance driver engagement—it streamlined communications between dispatch and the road, improving supply chain performance.
"TXI was the right partner to help us build our first mobile solution," said Jeff Yin, VP of Technology at Motorcity Systems.
With real-time data flow between drivers, dispatchers, and back-office systems, Motorcity made its operations more responsive and efficient. The solution incorporates supply chain analytics to optimize routing and scheduling, resulting in continuous improvements in delivery performance and fuel efficiency.
Building an Intelligence-Driven Manufacturing Organization
So how do you move from data collection to data intelligence?
Start by aligning your data goals with business objectives. Focus not on data volume but on outcomes like improved efficiency, reduced downtime, or higher product quality. Developing a cohesive data strategy that connects directly to your business priorities helps ensure that intelligence initiatives deliver tangible value.
Start Small and Iterate
Rather than attempting wholesale transformation, begin with focused initiatives that address specific pain points. Let value to the business be your guide. A food processor started with just one production line, using supply chain analytics to optimize inventory levels. After demonstrating a 15% reduction in raw materials inventory while maintaining production targets, they earned leadership buy-in to expand the approach across all product lines.
This incremental approach provides several advantages:
Lower initial investment and risk
Faster time to demonstrable results
Opportunity to learn and refine approaches
Building internal expertise and champions
Gaining organizational momentum and support
Build Cross-Functional Teams
Build cross-functional teams that bridge operations, IT, and leadership, ensuring insights flow across the organization. Manufacturing intelligence spans traditional boundaries, and siloed approaches rarely succeed.
Create Feedback Loops
Create feedback loops that refine strategies over time, and establish clear decision protocols to know when to automate and when human oversight is essential.
Foster a Data-Driven Culture
Finally, foster a culture of curiosity and action. Encourage your teams to ask: What is our data telling us? How can we use it to improve today? Data literacy initiatives play a critical role in this cultural transformation, creating an environment where decisions are increasingly driven by evidence rather than intuition.
These steps help manufacturers evolve from reactive data collection to proactive intelligence application, turning data into a strategic asset rather than an operational burden.
Conclusion: It's What You Do With It
Manufacturing intelligence isn't about accumulating more data. It's about using that data to drive better decisions.
As the manufacturing industry grows more complex and competitive, the ability to transform manufacturing data into intelligence becomes increasingly crucial. The competitive advantage comes not from having data—almost everyone has that—but from creating and applying intelligence that drives better decisions and outcomes.
Manufacturing intelligence isn't just about knowing what happened—it's about understanding why it happened, predicting what will happen next, and taking the right actions at the right time. This progression from descriptive to diagnostic to predictive to prescriptive capabilities represents the maturity journey for manufacturing analytics.
By turning information into actionable insights, manufacturers can gain agility, improve efficiency, and outpace competitors. The companies that succeed aren't the ones with the most dashboards — they're the ones making the most of their data.
In an era where manufacturing technology expertise is increasingly accessible, even mid-sized manufacturers can implement sophisticated intelligence solutions without massive in-house IT departments. The key is focusing on business outcomes rather than technology for its own sake.
If you're ready to put your data to work and unlock the full potential of manufacturing intelligence, let's start the conversation.
About the author
Alan Gardner is a Lead Engineer at TXI in Chicago, where he leads the architecture and implementation of bespoke applications and infrastructure solutions. He specializes in crafting strategic insights and guiding engineering teams to help organizations like yours make data-driven decisions.
Published by Alan Gardner in AI
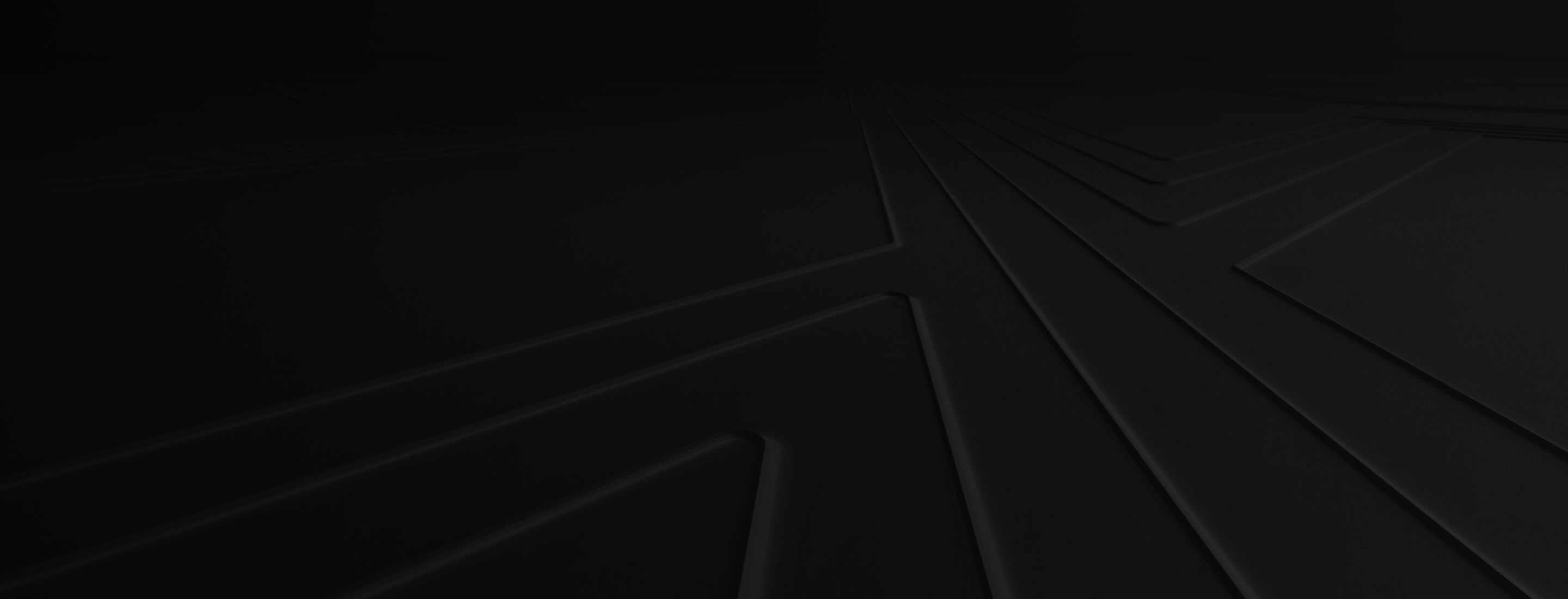
Let's shape your insights into experience-led data products together.