The future of manufacturing is being shaped by two critical factors: people and data integration. Here's what industry leaders are saying about navigating these challenges. Learn how workforce dynamics, data integration, and digital transformation are shaping the future of operations. Explore key insights on employee retention, knowledge management, data strategy, and the impact of technology on productivity. Get actionable recommendations for manufacturers looking to achieve step-change improvements in their business. Topics include blue-collar training, SaaS solutions, ERP implementations, and innovation initiatives.
Manufacturing’s crossroads: people, data, and the path forward
Key insights from the American Manufacturing Summit

Two weeks ago, our team attended the American Manufacturing Summit outside Chicago, where operations executives and plant managers gathered to discuss the evolving landscape of the manufacturing industry. As digital transformation initiatives continue to accelerate across the sector, a clear consensus emerged: the human element and data integration represent the most significant challenges—and opportunities—for manufacturers looking to gain a competitive edge.
The Workforce Revolution in Manufacturing
Manufacturing is experiencing an unprecedented shift in workforce dynamics. According to data shared at the conference from the Bureau of Labor Statistics, the average tenure in manufacturing organizations has plummeted from 20 years to just 5 years between 2019 and 2024. Even more concerning, the average 3-month retention rate has dropped from 90% to 50% during a similar timeframe.
These statistics tell a compelling story: despite significant investments in process improvements and technology, productivity has flatlined since 2010. The root cause? A growing gap in blue-collar training, skills development, and employee retention that effectively neutralizes the gains from continuous improvement efforts.
Industry leaders are now actively seeking new approaches to effectively run their operations, with particular interest in:
Innovative knowledge management systems
More effective training methodologies
Equipment optimization strategies
Several speakers noted that digital tools with strong user experience design are proving particularly effective in engaging and retaining younger, digitally native workers. This represents a significant shift in thinking for an industry that has traditionally focused on process and machinery over user experience. This echoes a trend we have seen over the past year, as we have experienced a marked increase in the number of clients wanting to rethink knowledge management and training.
Key Insight: High quality blue collar employee experiences (digital and physical) now plays a lynchpin role in unlocking operational productivity in manufacturing environments.
The Data Integration Challenge
Perhaps the most significant technical challenge highlighted at the conference was data management. The proliferation of narrow, use-case specific SaaS solutions has inadvertently widened the gap toward achieving a trusted, connected, and properly governed single source of truth.
Many manufacturers described their data journey as still in its early stages, with particular challenges in:
Connecting data between multiple operational systems
Establishing effective data governance frameworks
Cleaning and harmonizing metrics across systems
Building the foundation for more advanced analytics and AI applications
There was widespread recognition that high-quality, integrated data is fundamental to operational improvements and future innovation.
Key Insight: While SaaS / Off-the-shelf products highlighted AI all over the place, the megatrend was noticeably absent from our in-depth conversations with people who spend their days on the factory floor.
Digital Transformation: Different Paths, Common Challenges
While digital transformation remains a top priority across the manufacturing sector, approaches vary significantly depending on organizational context and timing of major systems implementations.
Some organizations, like Scotts Miracle Gro, are prioritizing advanced technologies such as robotics, drones, and image identification systems while deliberately postponing ERP implementations. Others, like Marmon Foodservice Technologies, advocate for establishing fundamental systems like ERP consistency before pursuing more innovative solutions.
The human element emerged as the most formidable challenge in digital transformation efforts. Speakers consistently emphasized change management and adoption programs as critical components of successful transformation journeys. Companies that excelled in this area demonstrated an ability to track adoption, build momentum through early wins, and focus on enterprise-wide impact.
Across all organizations, it is clear that manufacturers who layer digital transformation initiatives on top of a culture of continuous improvement are seeing multiplied effects from both efforts.
Looking Forward
The conference reinforced that Digital Transformation represents a significant opportunity for manufacturers willing to address these foundational challenges. Organizations that can successfully navigate workforce transformation while building robust data foundations will be positioned to achieve step-change improvements rather than incremental gains.
Based on the conference insights and our experience, we recommend manufacturing executives take the following specific actions:
Rethink your Employee Experience
Revamp onboarding processes to be more digitally-enabled and experiential, reducing time-to-productivity for new employees
Implement knowledge capture systems that document institutional knowledge from experienced workers before they depart
Design digital tools with UX as a priority, not just functionality—remember that good design drives adoption and retention
Assess your Digital Transformation
- If you are in the midst of an ERP implementation:
Establish robust change management programs with dedicated resources and executive sponsorship
Acknowledge that your innovation initiatives will take a back seat for the majority of your planning horizon
- If you are not in the midst of an ERP implementation:
Categorize your KPIs into innovation vs. continuous improvement candidates
Develop separate approaches to manage innovation and continuous improvement projects (e.g., create an innovation governance methodology)
For innovation projects, aim as high as possible!
Develop a Data Strategy
Prioritize use cases, usually found at the intersection of big decisions and inefficient analysis
Assess the data landscape by identifying critical data assets and integration points for the key use case
Establish clear data governance protocols with assigned ownership and accountability
Focus on foundational data quality by addressing issues at their source rather than through downstream corrections
Create the relevant data products that deliver actionable insights to the right people at the right time
The manufacturers who thrive in the coming years will be those who approach these challenges holistically, recognizing that people, processes, and technology must evolve together to realize the full potential of their business.
Published by Adam Schanfield , Jason Hehman in Industry 4.0
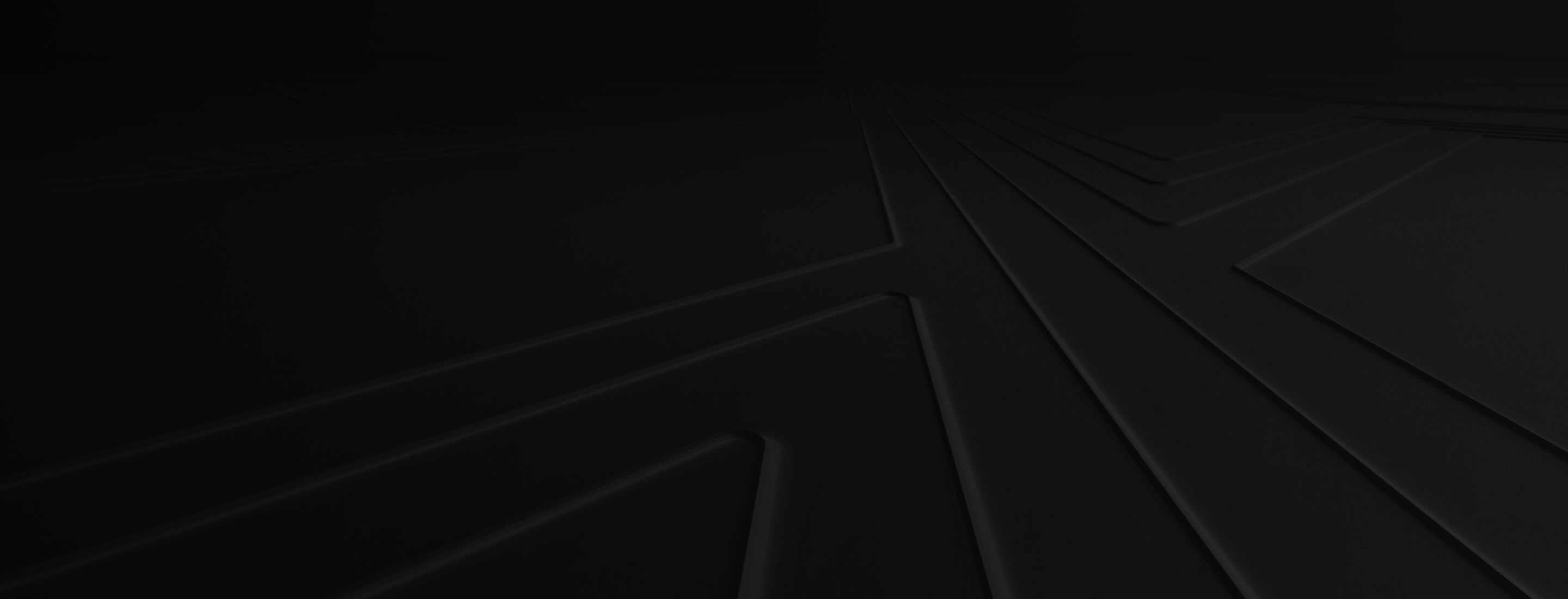
Let's shape your insights into experience-led data products together.