Inside a global giant’s digital transformation process
Modern Industrialist Podcast

Powered by RedCircle
Inside a Global Giant’s Digital Transformation Process
Tim O’Neal has a bird’s-eye view of digital transformation projects in manufacturing plants across the world. Tim is the Global Operations Director for Operational Excellence and Leveraged Services for Dow Chemical, overseeing digital transformation projects at over 300 plants in 31 different countries.
Here are his top insights for any manufacturing leader, no matter how big or small their production.
Understand the Problem
First, Tim says, understand the problem you’re trying to solve. Don’t just add new technology for the sake of adding new technology. Collect data on what the problem is. Make sure that data is accurate and meaningful. Evaluate proposed new tech based on how it addresses the problem, as described by the data. Then evaluate the tech again once you have performance data from usage.
People Process
Pay attention to the intersection of people and technology, says Tim. New technology isn’t going to be used in a vacuum. It’s going to be used by real people in real workplace cultures.
If you’re trying to figure out where to test new technology, take into consideration where people are eager to try it out. You can also develop eagerness by explaining to folks what the new technology’s end benefit to them will be.
Keep in mind that there’s less friction when new workplace technology is similar to the consumer technology that workers already use. For example, younger workers tend to use tablets with ease.
Start Small
Before you sink a ton of money into a massive digital transformation project, do small pilots. Tim encourages leaders to listen to feedback from beta users. It’s ok for a pilot to fail. It’s ok to wait until another iteration of a new technology. The value is in the experimentation and growth mindset.
Now is a unique time for digital transformation in manufacturing, according to Tim. Based on his experience on the Board of Governors for the Manufacturing Leadership Council (MLC), Tim sees that major players are cooperating with each other, sharing information and lessons learned in this early stage of digital transformation because they haven’t yet settled into proprietary, competitive technology. Now is the best time for manufacturers of all shapes and sizes to learn more about digital transformation.
Produced by NOVA Media
Book a meeting with Jason
Summary and themes explored in this episode:
Introduction and Background:
The episode begins with host Jason Heeman, TXI's Industry 4.0 Vertical Lead, introducing co-host Patrick Turley and guest Tim O'Neill, Global Operations Director at Dow Chemical.
Dow Chemical’s history and scale: Operating across 31 countries with 36,000 employees and $45 billion in sales in 2023, Dow is a leading force in material science.
Focus of the episode: Exploring Dow’s journey in digital transformation, operational excellence, and leveraging technology for innovation in manufacturing.
Dow’s Impact and Scale:
Tim explains Dow’s role in providing core materials for various industries, including plastics, automotive, and construction, acting as the “hard-working brand” behind many products.
Overview of Dow’s vast operations, including 98 manufacturing sites and over 300 production plants.
Tim’s Career and Role at Dow:
Tim’s journey from Union Carbide to Dow, spanning environmental health, safety, production leadership, and operational excellence roles.
His role focuses on ensuring best practices across people, processes, and technology to enhance efficiency and safety.
Importance of Foundation in Digital Transformation:
Emphasis on the need for a solid data foundation before implementing AI and digital solutions.
Dow’s approach includes piloting new technology on a small scale before broader rollouts, ensuring data quality and governance.
Culture of Innovation and Change Management:
Discusses fostering a culture that adapts to continuous improvement and innovation.
Dow’s approach to adopting new technology involves a balance of proven methods with innovations, considering plant readiness and workforce adaptability.
Key Innovations in Dow’s Digital Manufacturing Program:
Initiatives like connected tablets, digital labs, and contractor management tools enhance real-time data access, streamline processes, and improve safety.
Wireless and private LTE are introduced to sites to facilitate connectivity, especially for remote monitoring and data collection.
Challenges of AI in Manufacturing:
Tim highlights the cautious approach to AI and digitalization, acknowledging the need for quality data and effective change management.
Discussion on generative AI’s potential in capturing institutional knowledge and supporting operational decisions, while recognizing its limitations.
Emphasis on Learning and Training:
Dow's approach to training is evolving, integrating video, augmented reality, and virtual reality to better suit a tech-savvy workforce.
The goal is to make training more engaging and efficient, with experts in adult education leading this transformation.
Industry Leadership and Role Models:
Tim names David Brousell, founder of the Manufacturing Leadership Council (MLC), and Dow CEO Jim Fitterling as significant industry role models.
- The MLC is praised for fostering collaboration and innovation across the manufacturing sector.
Final Thoughts and Future Directions:
Tim’s commitment to advancing digital transformation in manufacturing and the value of data as a foundation for innovation.
- Jason and Patrick reflect on Tim’s insights, highlighting the importance of data-driven decision-making and empowering individuals through technology.
Produced by NOVA
Published by Jason Hehman , Patrick Turley in podcasts
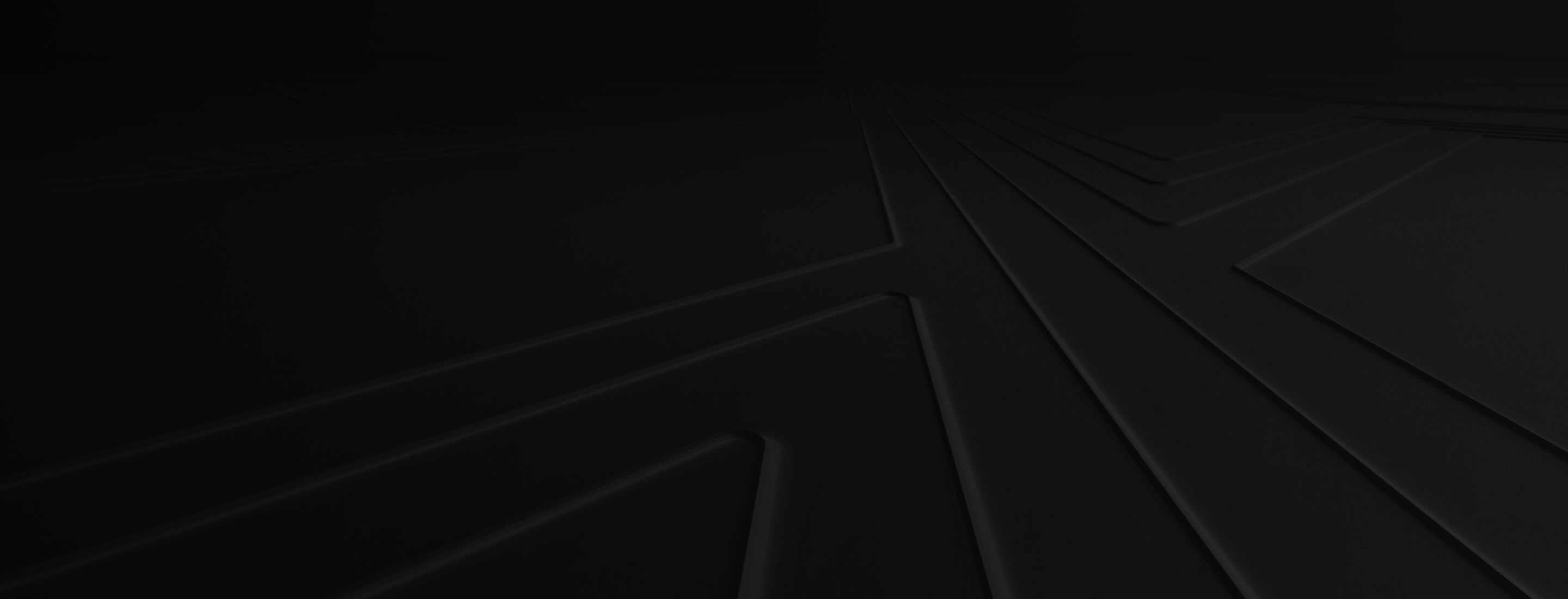
Let's shape your insights into experience-led data products together.